An inventory stock management system is how businesses control and manage their non-capitalized assets, inventories, and stock items. It regulates the flow of all goods from manufacturers to warehouses and final points of sale. Every business has the opportunity to monitor the flow of goods at any time by utilizing an inventory stock management system.
This process keeps a detailed record of every new receipt or return, ensuring the flow of goods in and out of storage facilities or points of sale. Proper inventory control supports businesses to use the correct goods in the right quantities, in the appropriate place, and at the best time.
Various inventory management techniques are available for this. Choosing the right method increases the efficiency and profitability of the business. In addition, using inventory management software in controls is much more contemporary compared to manual processes. It allows you to save time.
4 Types of Inventory Management System
Businesses need to have a proven inventory management system to grow and survive in a competitive market. Superior stock management cuts costs, boosts margins, and delivers long-term client happiness. There are 4 different inventory control systems available to better manage this important process.
JIT (Just-in-Time) Methodology
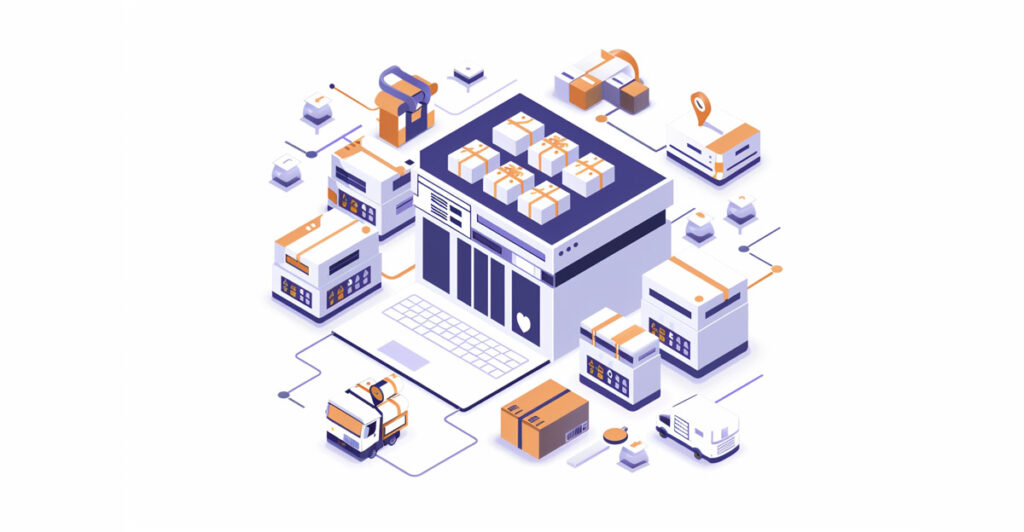
JIT methodology is a method in which products arrive when they are ordered by customers, and their behavior is precisely analyzed. It involves examining buying habits, seasonal demand, and location-dependent factors by accurately determining which products are in demand in specific periods and specific locations.
The main advantage of JIT is that customer demand can be met without the need to hold large amounts of inventory. However, there are also risks, such as misjudging market demand or distribution problems. This leads to an excess or shortage of stock.
ABC Analysis
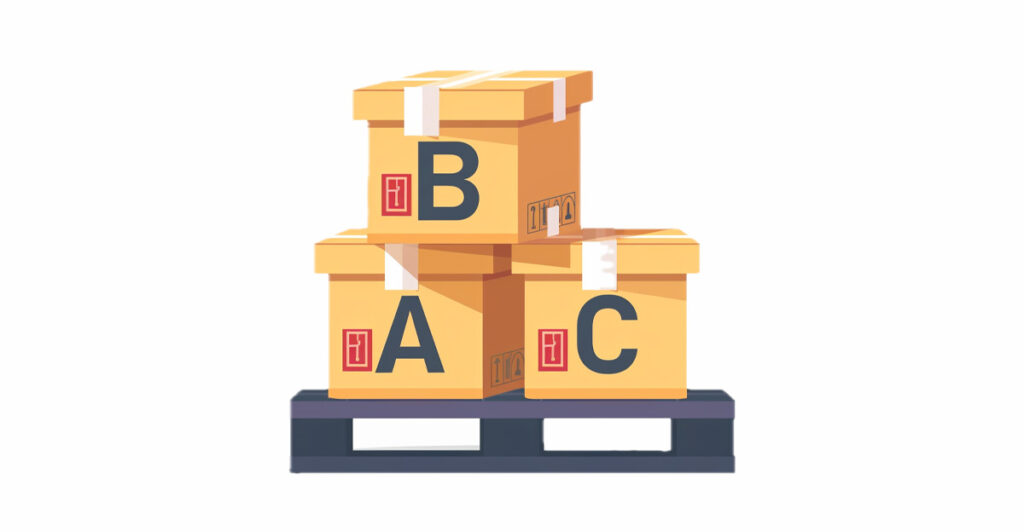
ABC analysis enables the qualified control of inventory by classifying goods into three categories representing their stock value and cost importance:
Category A
- Includes high-value goods and is underweighted.
- This category represents strategically important products. It should be subject to detailed stock management.
Category B
- Contains goods of medium value and medium weight.
- Includes products with stable demand. Requires careful planning.
Category C
- Includes goods of low value but high weight.
- Requires frequent replenishment of inventory.
This method of analysis requires a significant amount of resources as it requires continuous monitoring of the stock levels of each category.
EOQ
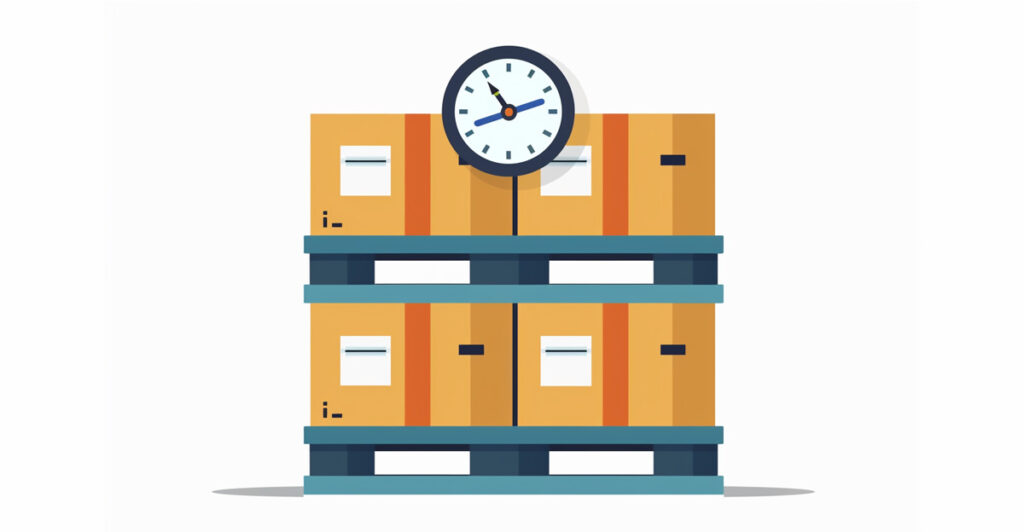
Economic Order Quantity (EOQ) methodology, a method for determining the optimal time to reorder inventory, is of great importance in warehouse control systems. Its main purpose is to minimize unnecessary costs by determining the optimal amount of products to be ordered in any time interval. By using it in warehouse management, financial losses are prevented and the costs of the business are minimized.
Inventory Management Software
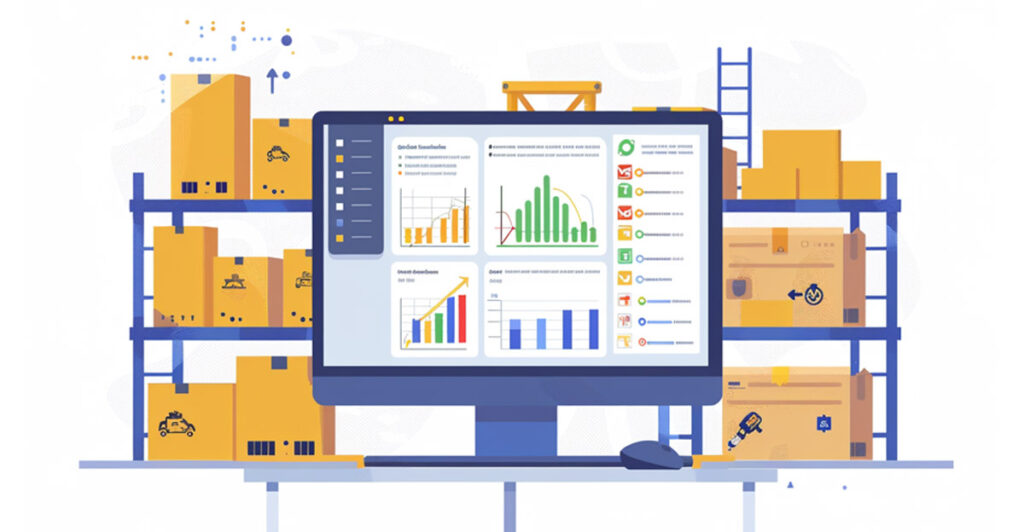
Inventory management software is easily one of the most prevalent systems utilized by today’s enterprises. The software automates many functions, such as stock tracking, order control, and reporting. With data analysis and forecasting capabilities, an inventory manager can manage stock more efficiently and respond quickly to demand.
Since every business has different needs, choosing the right inventory stock management system is vital. The most appropriate stock control solution should be determined by taking into account the scale, sector, and goals of your business. This will increase productivity, reduce costs, and ensure customer satisfaction.